SCREEN
MAKER
FAST SCREEN
TRACER
Today, The one thing all printing work have in common is that it has to be completed quickly. New digital screen making technology that does away with the need for emulsion paints a bright future for our customers.
With this state of the art technology,
screens can be made in a matter of minutes.
Upload data from the computer to the screen making machine, send print instructions — and the screen is ready before you know it. With conventional screen making technology involving emulsion sheets, creating a single screen can take three hours or more. With digital screen printing, it can take a mere two minutes. Digital screen printing supports a variety of data formats, from PDF and PNG to TIFF and BMP.
/
03
No segmentation means
the image does not shift.
With standard 100 mm thermal heads, the segmentation of the image can cause it to shift. With OHTAS’ digital screen making machines, which are quipped with thermal heads with a range of 35mm, this problem is now a thing of the past. Digital screen making with 355 mm thermal heads leads to results that are so fine that you have to see them to believe them.
/
03
Environmentally friendly
and people-friendly.
When it comes to environmental impact, digital screen making also has an advantage over emulsion sheets. Without the use of emulsion, it is not required to wash the screens; and ultimately no wastewater produced. Digital screen making also does away with the need to buy emulsion. However, even more valuable than that is the sheer amount of time that digital screen making saves.
/
03
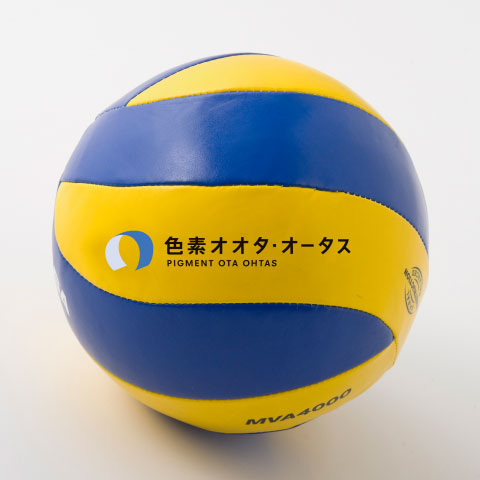
Silk screen printing allows for printing on spheres, a difficult surface to handle for other printing methods. In manufacturing processes, silk screen printing is used to print on objects such as balls and helmets. Customers greatly value the easy of use that screens offer.
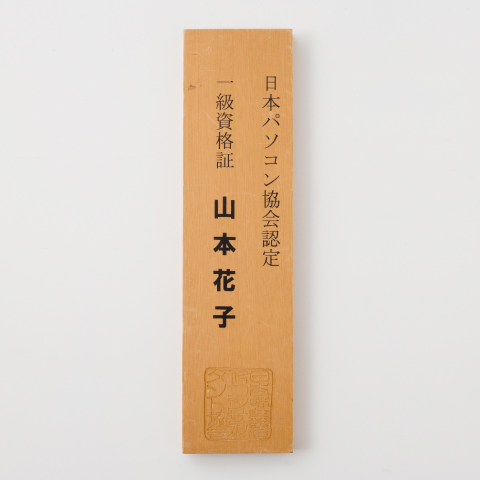
The FAST SCREEN TRACER is perfect for printing nameplates and other items of which someone may need only a single copy. Unlike with emulsion sheets, digital screens allow for optimal use of empty spaces on screens where there is room to squeeze in other designs. That can mean a significant reduction in costs.
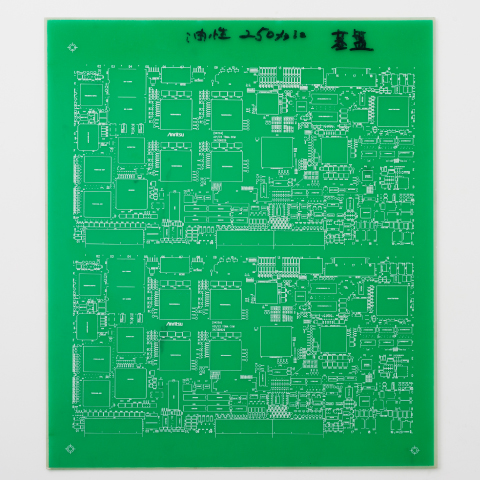
With conventional digital screen making systems, printing with solvent-based inks means reduced durability. The result is that, for example, the sheets cannot be used to make samples. However, our film will be fine after fifty printings and ten washings with solvent. Our film’s performance is truly exceptional compared to films used by other companies, and it makes printing with solvent-based inks a breeze.
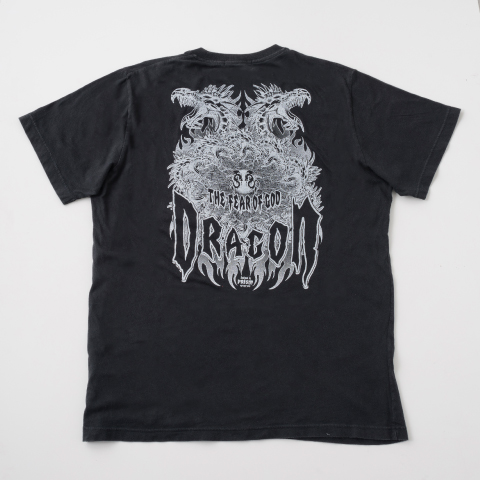
Digitally-made screens are cheaper and faster to produce than conventional screens made with emulsion sheets. Most of our customers take advantage of this to print on textured products such as original T-shirts. Digital screen making also enables people to meet short deadlines because the lead time is so short. Printing can begin within ten minutes of receiving the data. Of course, the cost of the screens themselves is also significantly less than those made with emulsion sheets.
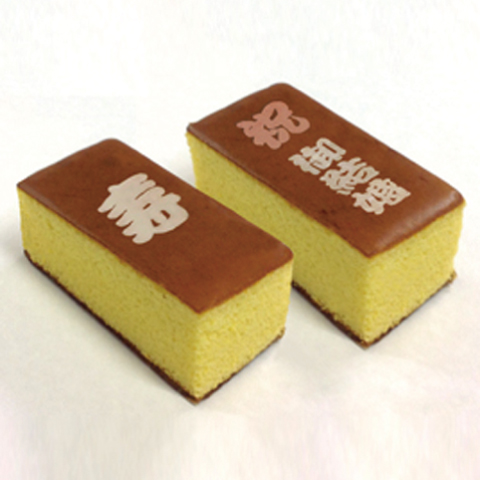
With edible dyes and the like, it is even possible to print on foodstuffs such as baked goods and cakes.
Equipment information
- Model name
- FAST SCREEN TRACER
- Machine size
- 600mm × 930mm × 254mm
- Weight
- 35kg
- Maximum frame size
- 500mm × 660mm × 30mm
- Maximum screen size
- 355mm × 480mm
- Resolution
- 320dpi × 320dpi( standard )、320dpi × 640dpi( high definition )
- Time to make a screen
- Approx. 1 min. 35 sec.( standard )、approx. 3 min. 10 sec.( high definition )
- Imaging speed
- Approx. 5.0 mm/sec.( standard )、approx. 2.5 mm/sec.( high definition )
Data environment
- Supported operating systems
- Windows 10 or later
- Connectivity
- USB2.0
- Data formats
- PDF/BMP/TIFF/PNG
Operating environment
- Voltage
- AC85-264V
- Frequency
- 50/60Hz(47〜63Hz)
- Power consumption
- 16W(at standby)/ 330W(at maximum operation)
- Temperature
- Storage temperature:-20〜70℃ 、 operating temperature:0℃〜50℃
- Humidity
- 20〜90%RH(only if no condensation is present)
Download